[ad_1]
By John P. Desmond, AI Traits Editor
Extra firms are efficiently exploiting predictive upkeep methods that mix AI and IoT sensors to gather information that anticipates breakdowns and recommends preventive motion earlier than break or machines fail, in an illustration of an AI use case with confirmed worth.
This development is mirrored in optimistic market forecasts. The predictive upkeep market is sized at $6.9 billion right this moment and is projected to develop to $28.2 billion by 2026, in line with a report from IoT Analytics of Hamburg, Germany. The agency counts over 280 distributors providing options available in the market right this moment, projected to develop to over 500 by 2026.
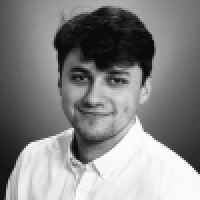
“This analysis is a wake-up name to those who declare IoT is failing,” acknowledged analyst Fernando Bruegge, writer of the report, including, “For firms that personal industrial property or promote tools, now’s the time to spend money on predictive maintenance-type options.” And, “Enterprise expertise corporations want to arrange to combine predictive upkeep options into their choices,” Bruegge instructed.
Here’s a evaluation of some particular expertise with predictive upkeep methods that mix AI and IoT sensors.
Plane engine producer Rolls-Royce is deploying predictive analytics to assist scale back the quantity of carbon its engines produce, whereas additionally optimizing upkeep to assist prospects hold planes within the air longer, in line with a latest account in CIO.
Rolls-Royce constructed an Clever Engine platform to watch engine flight, gathering information on climate circumstances and the way pilots are flying. Machine studying is utilized to the information to customise upkeep regimes for particular person engines.

“We’re tailoring our upkeep regimes to ensure that we’re optimizing for the life an engine has, not the life the guide says it ought to have,” acknowledged Stuart Hughes, chief data and digital officer at Rolls-Royce. “It’s really variable service, taking a look at every engine as a person engine.”
Prospects are seeing much less service interruption. “Rolls-Royce has been monitoring engines and charging per hour for not less than 20 years,” Hughes acknowledged. “That a part of the enterprise isn’t new. However as we’ve advanced, we’ve begun to deal with the engine as a singular engine. It’s way more concerning the personalization of that engine.”
Predictive analytics is being utilized in healthcare in addition to within the manufacturing business. Kaiser Permanente, the built-in managed care consortium primarily based in Oakland, Calif. Is utilizing predictive analytics to establish non-intensive care unit (ICU) sufferers liable to speedy deterioration.
Whereas non-ICU sufferers that require surprising transfers to the ICU represent lower than 4% of the full hospital inhabitants, they account for 20% of all hospital deaths, in line with Dr. Gabriel Escobar, analysis scientist, Division of Analysis, and regional director, Hospital Operations Analysis, Kaiser Permanente Northern California.
Kaiser Permanente Practising Predictive Upkeep in Healthcare
Kaiser Permanente developed the Superior Alert Monitor (AAM) system, leveraging three predictive analytic fashions to investigate greater than 70 elements in a given affected person’s digital well being file to generate a composite threat rating.
“The AAM system synthesizes and analyzes very important statistics, lab outcomes, and different variables to generate hourly deterioration threat scores for grownup hospital sufferers within the medical-surgical and transitional care items,” acknowledged Dick Daniels, government vp and CIO of Kaiser Permanente within the CIO account. “Distant hospital groups consider the chance scores each hour and notify speedy response groups within the hospital when potential deterioration is detected. The speedy response crew conducts bedside analysis of the affected person and calibrates the course therapy with the hospitalist.”
In recommendation to different practitioners, Daniels beneficial a give attention to how the instrument might be match into the workflow of well being care groups. “It took us about 5 years to carry out the preliminary mapping of the digital medical file backend and develop the predictive fashions,” Daniels acknowledged. “It then took us one other two to a few years to transition these fashions right into a stay net companies software that may very well be used operationally.”
In an instance from the meals business, a PepsiCo Frito-Lay plant in Fayetteville, Tenn. is utilizing predictive upkeep efficiently, with year-to-date tools downtime at 0.75% and unplanned downtime at 2.88%, in line with Carlos Calloway, the location’s reliability engineering supervisor, in an account in PlantServices.
Examples of monitoring embody: vibration readings confirmed by ultrasound helped to stop a PC combustion blower motor from failing and shutting down the entire potato chip division; infrared evaluation of the principle pole for the plant’s GES automated warehouse detected a sizzling fuse holder, which helped to keep away from a shutdown of the whole warehouse; and elevated acid ranges had been detected in oil samples from a baked extruder gearbox, indicating oil degradation, which enabled prevention of a shutdown of Cheetos Puffs manufacturing.
The Frito-Lay plant produces greater than 150 million kilos of product per 12 months, together with Lays, Ruffles, Cheetos, Doritos, Fritos, and Tostitos.
The forms of monitoring embody vibration evaluation, used on mechanical functions, which is processed with the assistance of a third-party firm which sends alerts to the plant for investigation and determination. One other service associate performs quarterly vibration monitoring on chosen tools. All motor management middle rooms and electrical panels are monitored with quarterly infrared evaluation, which can also be used on electrical tools, some rotating tools, and warmth exchangers. As well as, the plant has finished ultrasonic monitoring for greater than 15 years, and it’s “form of just like the satisfaction and pleasure of our website from a predictive standpoint,” acknowledged Calloway.
The plan has a variety of merchandise in place from UE Methods of Elmsford, NY, provider of ultrasonic devices, {hardware} and software program, and coaching for predictive upkeep.
Louisiana Alumina Plant Automating Bearing Upkeep
Bearings, which put on over time underneath various circumstances of climate and temperature within the case of vehicles, are a number one candidate for IoT monitoring and predictive upkeep with AI. The Noranda Alumina plant in Gramercy, La. is discovering a giant payoff from its funding in a system to enhance the lubrication of bearings in its manufacturing tools.
The system has resulted in a 60% decline in bearing modifications within the second 12 months of utilizing the brand new lubrication system, translating to some $900,000 in financial savings on bearings that didn’t must be changed and prevented downtime.
“4 hours of downtime is about $1 million {dollars}’ price of misplaced manufacturing,” acknowledged Russell Goodwin, a reliability engineer and millwright teacher at Noranda Alumina, within the PlantServices account, which was primarily based on shows on the Main Reliability 2021 occasion.
The Noranda Alumina plant is the one alumina plant working within the US. “If we shut down, you’ll must import it,” acknowledged Goodwin. The plant experiences pervasive mud, dust, and caustic substances, which complicate efforts at improved reliability and upkeep practices.
Noranda Alumina tracks all motors and gearboxes at 1,500 rpm and better with vibration readings, and most beneath 1,500 with ultrasound. Ultrasonic monitoring, of sound in ranges past human listening to, was launched to the plant after Goodwin joined the corporate in 2019. On the time, grease monitoring had room for enchancment. “If grease was not visibly popping out of the seal, the mechanical supervisor didn’t rely the spherical as full,” acknowledged Goodwin.
After introducing automation, the greasing system has improved dramatically, he acknowledged. The system was additionally in a position to detect bearings in a belt whose bearings had been carrying out too shortly as a consequence of contamination. “Software-enabled monitoring helped to show that it wasn’t improper greasing, however quite the bearing was made improperly,” acknowledged Goodwin.
Learn the supply articles and data in IoT Analytics, in CIO and in PlantServices.
[ad_2]